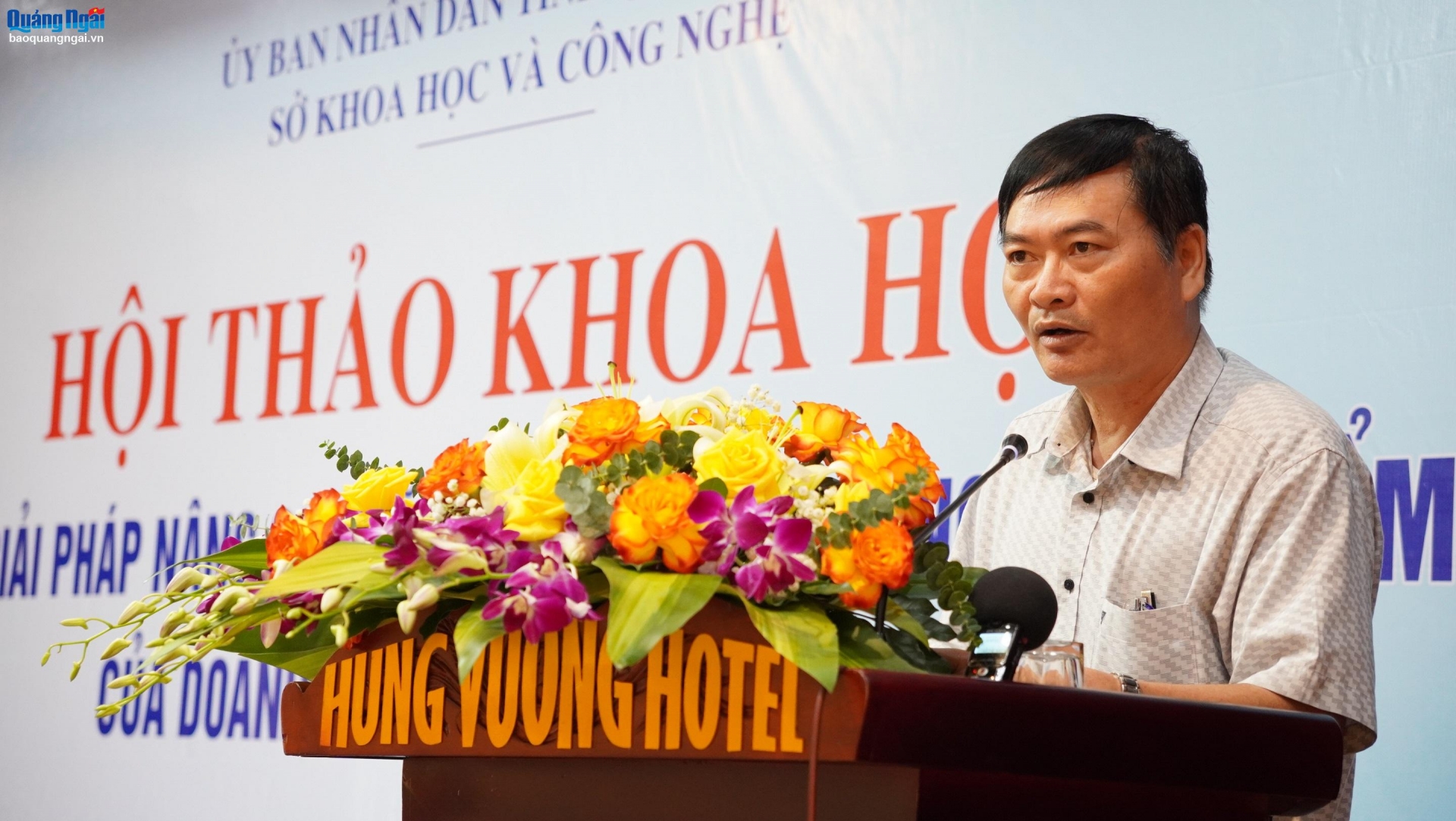
21/09/2024
Trong khuôn khổ Chương trình hỗ trợ thành lập Câu lạc bộ năng suất chất lượng trong sinh viên các trường đại học, cao đẳng, chiều ngày 20/9/2024, Ủy ban Tiêu chuẩn Đo lường Chất lượng Quốc gia đã tổ chức buổi đào tạo với chuyên đề 9: “Lean: Tư duy giảm thiểu lãng phí (Lean) để tăng năng suất”.
Về phía Ủy ban, chương trình có sự tham gia của ông Phạm Lê Cường – Phó Chánh Văn phòng, đoàn viên, thanh niên các đơn vị của Ủy ban tham dự trực tiếp và trực tuyến.
Về phía các trường đại học, cao đẳng có sự tham gia trực tuyến của gần 100 sinh viên và các thầy cô giáo đến từ: Đại học Phan Thiết, Đại học Nha Trang, Đại học Trà Vinh, Đại học Kinh tế – Đại học Quốc gia Hà Nội, Học viện Báo chí và Tuyên truyền, Đại học Bình Dương, Đại học Lâm Nghiệp, Đại học Kinh tế kỹ thuật Thái nguyên, Đại học Thủ Dầu 1, Cao đẳng Công nghệ Việt – Hàn Bắc Giang, Đại học Công nghiệp Dệt May Hà Nội, Cao đẳng Nghề Việt Xô số 1 Vĩnh Phúc, Cao đẳng Miền núi Bắc Giang, Cao đẳng Công nghiệp và Xây dựng Quảng Ninh, Cao đẳng Nghề Sóc Trăng.
Trình bày tại buổi đào tạo ThS. Đỗ Thu Hương – Ủy viên Ban Chấp hành Đoàn thanh niên Ủy ban Tiêu chuẩn Đo lường Chất lượng Quốc gia cho biết, Lean được biết đến là mô hình quản trị theo triết lý tinh gọn. Từ những năm 1930 – khởi nguồn từ hệ thống sản xuất của Toyota: Taiichi Ohno, một kỹ sư tại Toyota, bắt đầu nghiên cứu và phát triển hệ thống sản xuất mới, ông quan sát và học hỏi từ cách thức sản xuất của các nhà máy ô tô Mỹ, đặc biệt là Ford. Mục tiêu là tối ưu hóa quy trình, loại bỏ mọi lãng phí và tăng năng suất.
Những năm 1950 – Xây dựng và phát triển hệ thống sản xuất Toyota (TPS): Ohno và Shigeo Shingo tiếp tục hoàn thiện và triển khai TPS tại các nhà máy của Toyota. TPS trở thành nền tảng cho việc sản xuất ô tô hiệu quả của Toyota.
Những năm 1970-1980 – Lan rộng ra thế giới: Hệ thống sản xuất của Toyota bắt đầu được các công ty ô tô khác quan tâm và học hỏi. Các nguyên lý và công cụ của TPS dần được áp dụng rộng rãi trong các ngành công nghiệp khác.
Những năm 1990 – Được định nghĩa và hệ thống hóa: Thuật ngữ “Lean manufacturing” lần đầu tiên xuất hiện vào năm 1990, trong quyển The Machine that Changed the World (Cỗ máy làm thay đổi cả thế giới).
Hiện nay có 7 loại lãng phí bao gồm sản xuất dư thừa, tồn kho quá mức, vận chuyển, chờ đợi, thao tác thừa không cần thiết, khuyết tật và phế phẩm, quá trình gia công không phù hợp.
Về loại lãng phí thứ nhất do sản xuất dư thừa, nguyên nhân do dự báo sai nhu cầu; Dư thừa nhân công hoặc công suất thiết bị nhưng vẫn sản xuất liên tục; Muốn có hàng dự phòng để đáp ứng nhanh nhu cầu của khách hàng.
Về giải pháp cần sự phối hợp tốt hơn giữa các phòng ban để sản xuất một lượng phù hợp vừa đáp ứng nhu cầu của khách hàng, vừa tránh được lãng phí do sản xuất dư thừa.
Lãng phí thứ 2 do tồn kho, nguyên nhân do sản xuất quá mức: làm sớm hoặc nhiều hơn nhu cầu của khách hàng; Thiếu cân bằng trong dòng chảy sản xuất: sản xuất không liên tục, tắc nghẽn dẫn đến tồn kho ở trước hoặc sau các công đoạn; Lo ngại không đáp ứng yêu cầu của khách hàng.
Nguyên nhân khác: Đầu tư quá lớn và không đồng nhất vào máy móc, nhu cầu của khách hàng không ổn định, kế hoạch sản xuất không phù hợp…
Về giải pháp cần lên lịch trình sản xuất phù hợp dựa trên các đơn đặt hàng và chỉ sản xuất những gì khách hàng yêu cầu; Cân bằng dòng chảy sản xuất, tiết chế các công đoạn sản xuất; Tính toán, đặt hàng với số lượng phù hợp.
Lãng phí thứ 3 lãng phí do chờ đợi – trì hoãn, nguyên nhân do sự cố máy móc; Chờ đợi công đoạn trước hoàn thành; Cúp điện, máy tính chậm, chờ sếp duyệt…
Lãng phí thứ 4 do thao tác thừa, nguyên nhân do các chuyển động tay chân hay việc đi lại không cần thiết; Sắp xếp các file trong máy tính không hợp lý; Bố trí máy móc thiết bị, công cụ không phù hợp.
Lãng phí thứ 5 do vận chuyển là sự chuyển động nguyên vật liệu không tạo ra giá trị gia tăng cho sản phẩm: Trong sản xuất là việc vận chuyển nguyên phụ liệu đến dây chuyền sản xuất; trong dịch vụ là việc vận chuyển hàng hóa đến tay người tiêu dùng.
Không thể loại bỏ nhưng có thể rút ngắn khoảng cách, giảm thời gian và nguồn nhân lực cho vận chuyển.
Lãng phí thứ 6 do khuyết tật và phế phẩm là các khuyết tật về sản phẩm, sai sót về giấy tờ, thông tin, giao hàng chậm, sản xuất sai quy cách, sử dụng quá nhiều nguyên vật liệu hay tạo ra phế liệu không cần thiết.
Coi những người làm công đoạn sau là khách hàng để hoàn thành tốt công việc của mình. Tìm ra nguyên nhân gây lỗi để giải quyết triệt để vấn đề, ngăn ngừa lỗi xảy ra trong tương lai.
Lãng phí thứ 7 do quá trình gia công không phù hợp hoàn thiện quá mức.
Cũng theo bà Hương, 5 nguyên tắc của LEAN bao gồm: Xác định giá trị từ góc nhìn khách hàng; Xây dựng sơ đồ dòng giá trị; Tạo ra dòng chảy; Thiết lập hệ thống sản xuất theo nhu cầu; Cải tiến liên tục.
Các bước triển khai áp dụng Lean gồm: chuẩn bị khảo sát, xác định phạm vi và công cụ áp dụng, xác định giải pháp triển khai và áp dụng, kiểm soát, duy trì và tổng kết dự án.
Lợi ích của việc áp dụng LEAN sẽ làm tăng năng suất, giảm lãng phí, cải thiện hiệu quả, sản xuất nhiều hơn với ít nguồn lực hơn. Bên cạnh đó, giảm chi phí, loại bỏ hoạt động không tạo giá trị, tối ưu hóa sử dụng tài nguyên, tiết kiệm chi phí sản xuất; Cải thiện chất lượng, tập trung vào việc loại bỏ lỗi, nâng cao chất lượng sản phẩm, đáp ứng tốt hơn nhu cầu khách hàng. Ngoài ra, rút ngắn thời gian chu kỳ, giao hàng nhanh chóng, phản hồi nhanh với thay đổi thị trường, tăng khả năng cạnh tranh.
Tuy nhiên, cũng có những thách thức trong triển khai LEAN như kháng cự từ nhân viên: Nhân viên có thể không hiểu rõ về Lean. Họ có thể sợ hãi thay đổi và mất đi công việc của mình, thiếu sự tham gia của nhân viên, thiếu động lực. Bên cạnh đó là thiếu sự hỗ trợ từ lãnh đạo: Lãnh đạo cần hỗ trợ và ủng hộ việc triển khai Lean. Họ cần phải là những người tiên phong và dẫn dắt.
Chia sẻ về mối quan hệ giữa LEAN và chuyển đổi số, bà Hương cho hay LEAN và chuyển đổi số không phải hai khái niệm độc lập mà là hai khía cạnh hỗ trợ lẫn nhau. LEAN tối ưu hóa quy trình, loại bỏ lãng phí, nâng cao hiệu quả. Chuyển đổi số giúp tự động hóa quy trình, thu thập dữ liệu, và phân tích thông tin, tạo cơ sở cho LEAN hoạt động hiệu quả hơn.
Chuyển đổi số cung cấp công nghệ và dữ liệu để LEAN hoạt động hiệu quả hơn. LEAN tập trung vào cải tiến liên tục, tạo cơ hội cho Chuyển đổi số áp dụng các giải pháp mới, nâng cao hiệu quả. Cả hai cùng góp phần thúc đẩy sự phát triển bền vững và năng suất cao.
Buổi đào tạo “Lean: Tư duy giảm thiểu lãng phí (Lean) để tăng năng suất” là chuyên đề thứ 9 trong chuỗi 10 chuyên đề đào tạo về các công cụ cải tiến năng suất do báo cáo viên của Ủy ban trình bày, lần lượt bao gồm:
“Tổng quan về năng suất”;
5S – Nền tảng cải tiến năng suất chất lượng;
TWI – Mô hình nhóm huấn luyện (TWI) nâng cao năng lực cho đội ngũ giám sát tuyến đầu;
7 lãng phí – Nhận diện các lãng phí trong sản xuất và cách loại bỏ hiệu quả;
Kaizen – Tư duy cải tiến liên tục;
QCC – Nhóm kiểm soát chất lượng;
TPM – Áp dụng TPM nhằm cải thiện hiệu quả sử dụng máy móc, thiết bị;
MFCA – Tổng quan về MFCA: Phương pháp hạch toán chi phí dòng nguyên liệu;
Lean: Tư duy giảm thiểu lãng phí (Lean) để tăng năng suất;
KPI: Áp dụng KPI trong thực thi chiến lược kinh doanh của tổ chức.
Nguồn: vietq.vn