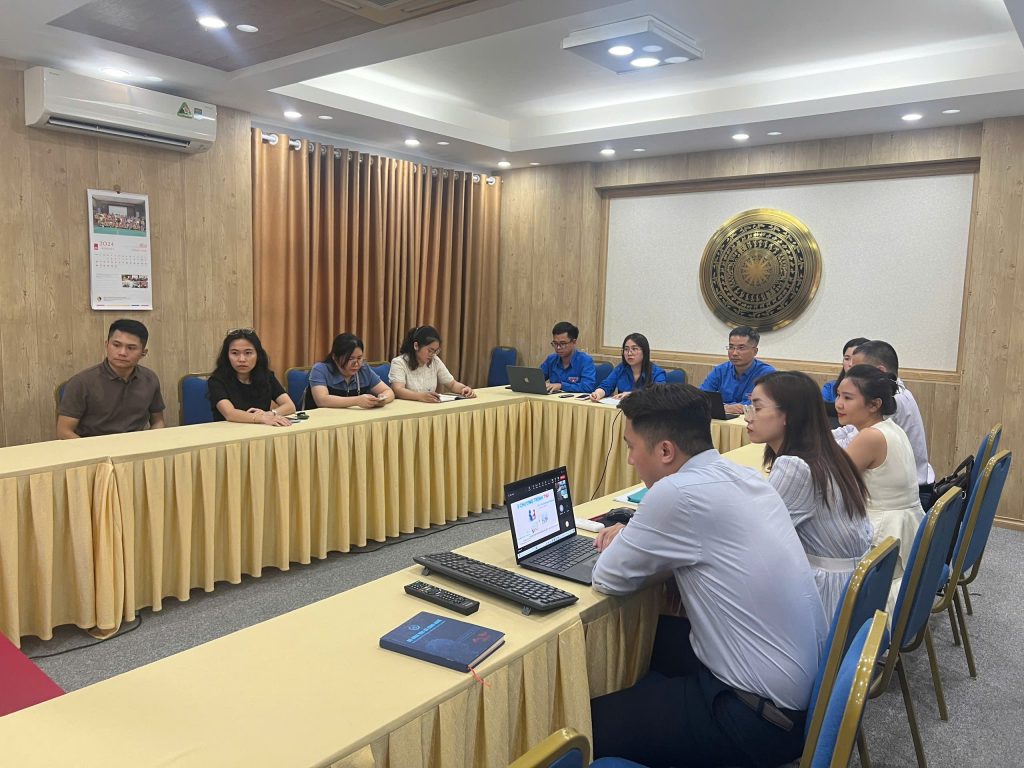
16/09/2024
Trong khuôn khổ Chương trình hỗ trợ thành lập Câu lạc bộ năng suất chất lượng trong sinh viên các trường đại học, cao đẳng, chiều ngày 16/9/2024, Ủy ban Tiêu chuẩn Đo lường Chất lượng Quốc gia đã tổ chức buổi đào tạo với chuyên đề 7: “TPM – Áp dụng TPM nhằm cải thiện hiệu quả sử dụng máy móc, thiết bị”.
Về phía Ủy ban, chương trình có sự tham gia của ông Phạm Lê Cường – Phó Chánh Văn phòng, đoàn viên thanh niên các đơn vị của Ủy ban tham dự trực tiếp và trực tuyến.
Về phía các trường đại học, cao đẳng có sự tham gia trực tuyến của gần 100 sinh viên và các thầy cô giáo đến từ: Đại học Phan Thiết, Đại học Nha Trang, Đại học Trà Vinh, Đại học Kinh tế – Đại học Quốc gia Hà Nội, Học viện Báo chí và Tuyên truyền, Đại học Bình Dương, Đại học Lâm Nghiệp, Đại học Kinh tế kỹ thuật Thái nguyên, Đại học Thủ Dầu 1, Cao đẳng Công nghệ Việt – Hàn Bắc Giang, Đại học Công nghiệp Dệt May Hà Nội, Cao đẳng Nghề Việt Xô số 1 Vĩnh Phúc, Cao đẳng Miền núi Bắc Giang, Cao đẳng Công nghiệp và Xây dựng Quảng Ninh, Cao đẳng Nghề Sóc Trăng.
Trình bày tại buổi đào tạo, ThS. Nguyễn Thị Thương – Phó Bí thư Đoàn Ủy ban Tiêu chuẩn Đo lường Chất lượng Quốc gia cho biết, là công cụ quản lý hiệu suất tổng thể, TPM (Total Productive Maintenance) đang trở thành một trong những giải pháp quan trọng được doanh nghiệp lựa chọn nhằm bảo đảm hiệu quả thiết bị, tối đa hóa hiệu suất, nâng cao năng suất, chất lượng sản phẩm và tạo môi trường làm việc an toàn.
Khi tìm hiểu về TPM, chúng ta cần phải chú ý 2 điều quan trọng: Thứ nhất, TPM nhấn mạnh việc bảo trì chủ động. Máy móc chỉ dừng khi chúng ta chủ động dừng nó trong kế hoạch bảo trì hệ thống, chứ không phải dừng khẩn cấp vì tai nạn hay sự cố hỏng hóc. Thứ hai, với TPM, mọi người cùng hợp lực và tương tác để nâng cao hiệu suất hoạt động của thiết bị một cách hiệu quả nhất. Suy nghĩ “trách nhiệm người vận hành là vận hành thiết bị, trách nhiệm của nhân viên bảo trì là sửa chữa” được thay bằng “Tôi và Anh cùng chịu trách nhiệm về thiết bị của Chúng ta, nhà máy của Chúng ta, tương lai của Chúng ta”.
TPM được hình thành và phát triển qua 4 giai đoạn, đầu tiên, trước năm 1951, chúng ta mới biết đến khái niệm “Bảo dưỡng sửa chữa”, khái niệm này có nghĩa là thiết bị chỉ được bảo dưỡng khi xảy ra sự cố hỏng hóc. Cho tới năm 1951, khái niệm “Bảo dưỡng phòng ngừa” mới bắt đầu được hình thành từ nước Mỹ.
Cho tới năm 1971, Viện Bảo dưỡng nhà máy Nhật Bản giới thiệu phương pháp TPM và một yếu tố quan trọng của TPM, Tự bảo dưỡng cũng bắt đầu xuất hiện từ đây.
Kể từ cuối thế kỷ 20, TPM đã trở thành một phần của xu hướng sản xuất tinh gọn, đi đôi với việc giảm lãng phí sản xuất và được hàng trăm công ty áp dụng, thực hiện trên khắp thế giới.
Cùng với xu hướng công nghiệp hóa, hoạt động bảo dưỡng đã trải qua những giai đoạn phát triển khác nhau, từ bị động đến chủ động với các loại bảo dưỡng chủ yếu:
Bảo dưỡng sửa chữa: Theo phương pháp này, hoạt động bảo dưỡng mang tính bị động, có nghĩa khi máy móc bị hỏng và ngừng hoạt động, công tác sửa chữa mới được thực hiện.
Bảo dưỡng phòng ngừa: Với phương pháp này, máy móc thiết bị được dừng hoạt động theo một chu kỳ nhất định để sửa chữa, thay thế phụ tùng, bảo dưỡng
Bảo dưỡng khắc phục: Hướng vào cải tiến thiết bị và các bộ phận nhằm tăng độ tin cậy, tuổi thọ của thiết bị.
Phòng ngừa bảo dưỡng: Áp dụng đối với thiết bị mới. Người thiết kế thiết bị cần nghiên cứu đầy đủ các điểm hạn chế của máy móc để ngăn ngừa hỏng hóc cũng như giúp việc bảo dưỡng dễ dàng hơn và ngăn ngừa lỗi của thiết bị.
Cũng theo bà Thương, có 7 lãng phí trong sản xuất, đó là: Vận chuyển, Tồn kho, Thao tác thừa, Chờ đợi, Quá trình, Sản xuất thừa, Khuyết tật.
Khi tìm hiểu về TPM, ngoài việc tìm hiểu về các lãng phí trong sản xuất, chúng ta cần quan tâm đến các tổn thất liên quan đến thiết bị. Bao gồm 6 tổn thất: Thiết bị lỗi hoặc hỏng hóc, Cài đặt và hiệu chỉnh thiết bị, Thiết bị chạy không tải và bị gián đoạn khi đang vận hành, Tốc độ vận hành bị giảm sút, Sản phẩm đầu ra bị khuyết tật, Hiệu suất thiết bị giảm sút – Những tổn thất khi khởi động máy. Tư duy “hư đâu sửa đó” là nguyên nhân chính gây nên “Sáu tổn thất lớn” của thiết bị và được xem là nguyên nhân cốt lõi làm cho thiết bị không đạt hiệu quả trong quá trình sản xuất.
Mục tiêu của TPM chính là xây dựng một công ty hoạt động khỏe mạnh hơn, hiệu quả hơn thông qua nâng cao hiệu quả thiết bị cũng như con người. Chính vì vậy, TPM có 4 mục tiêu chính là: Không có sự cố phải dừng máy để sửa chữa; Không có phế phẩm; Không có lãng phí; Nâng cao ý thức trách nhiệm và tinh thần làm chủ.
TPM được ví như một ngôi nhà, trong đó các nguyên tắc của TPM chính là hệ thống cột trụ của ngôi nhà đó. Các trụ cột của hoạt động TPM gồm: Bảo dưỡng tự chủ hoặc tự bảo dưỡng, Cải tiến có trọng điểm, Bảo dưỡng có kế hoạch, Duy trì chất lượng, Kiểm soát từ đầu, Đào tạo và huấn luyện, Hoạt động TPM tại khối văn phòng, An toàn, sức khỏe và môi trường. Bên cạnh các trụ cột trên, để thực hiện tốt TPM không thể thiếu hoạt động 5S. 5S được xem là nền móng của ngôi nhà TPM, khởi đầu cho việc phát hiện các vấn đề để tiến hành hoạt động cải tiến trong TPM.
Buổi đào tạo “TPM – Áp dụng TPM nhằm cải thiện hiệu quả sử dụng máy móc, thiết bị” là chuyên đề thứ 7 trong chuỗi 10 chuyên đề đào tạo về các công cụ cải tiến năng suất do báo cáo viên của Ủy ban trình bày, lần lượt bao gồm:
“Tổng quan về năng suất”;
5S – Nền tảng cải tiến năng suất chất lượng;
TWI – Mô hình nhóm huấn luyện (TWI) nâng cao năng lực cho đội ngũ giám sát tuyến đầu;
7 lãng phí – Nhận diện các lãng phí trong sản xuất và cách loại bỏ hiệu quả;
Kaizen – Tư duy cải tiến liên tục;
QCC – Nhóm kiểm soát chất lượng;
TPM – Áp dụng TPM nhằm cải thiện hiệu quả sử dụng máy móc, thiết bị;
MFCA – Tổng quan về MFCA: Phương pháp hạch toán chi phí dòng nguyên liệu;
Lean: Tư duy giảm thiểu lãng phí (Lean) để tăng năng suất;
KPI: Áp dụng KPI trong thực thi chiến lược kinh doanh của tổ chức.
Nguồn: vietq.vn